Facilitating a healthy atmosphere in the workplace
Indoor air gets cleaned in a natural way with the ionization process, which sterilizes the indoor air from microorganisms and VOCs. And this is the case at the Unilever Food Innovation Center in Wageningen, a municipality situated in the Dutch province of Gelderland, where ionair BeNeLux B.V. has installed six ionization systems in the ventilation plants of the multinational corporation. We talked to Jeroen Posthumus (45), Director of ionair BeNeLux B.V., to see how this order came about.
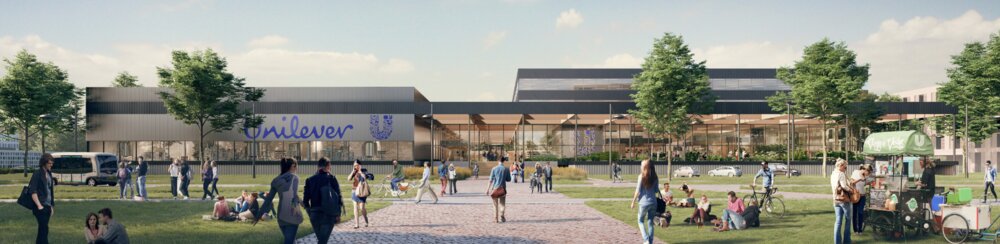
Jeroen – congratulations on getting the order. How did the request to install six ionization systems for a multinational corporation like Unilever Food come about?
Well, this group aspires to provide a comfortable and healthy atmosphere at the workplace for its employees. This is why Unilever is continuously investing in new «green» and environmentally-friendly buildings. The same applies to the new Unilever Food Innovation Center. Together with the office of the architect Paul de Ruiter, its technical consultants and the design workshop, DWA, it decided to install various air cleaning systems. These included, among other things, the «Air Quality System» (AQS) from ionair in the supply air ducts.
With the «Air Quality System» (AQS), the air quality and hygiene in the ventilated room gets significantly improved. What were the crucial arguments in favor of the AQS for the Unilever Group?
The ionization process demonstrably cleans the indoor air and therefore has a favorable impact on the quality of indoor air. A large number of VOCs (volatile organic compounds) are reduced, generally speaking by up to 50% thanks to the AQS. Often, the limit of odor perception is deep and this means that a few percentage points help in terms of generating a comfortable indoor air climate from annoying, poor quality air. Unilever aimed to achieve the highest BREEAM standard with the Food Center. This standard is the most widespread certification method for environmentally-friendly buildings. The certification is a de facto indicator for environmental standards and ionair was able to contribute to the certification with its process.
How did you approach such a project?
The installation of the six systems from ionair was carried out over a period of approximately five months and this involved a lot of coordination and organization. This presented us with a big challenge, despite the vast experience that we have in dealing with such large construction projects. In addition, the fitters in charge did an excellent job. They supported us on all matters and they ensured the material was always in the right place at the right time. In fact, the cooperation with the other companies involved in the construction was also really positive - everything was coordinated extremely well.
What has been the feedback from Unilever?
It is still too early for any definitive feedback as Unilever is currently in the process of relocating to the finished building. We will test the indoor air quality (IAQ) over the coming months in order to compare the measured values with those in other rooms that are not being ionized.
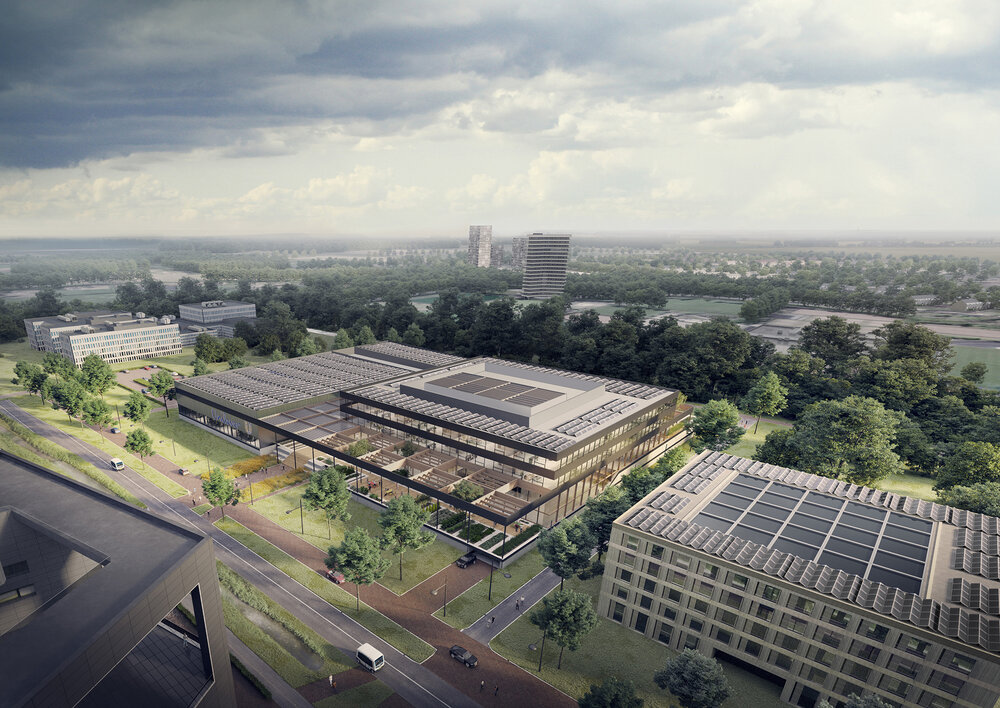